Vapor Corrosion Inhibitors (VCI) have proven to be a cost effective alternative to the traditional dry and N2 purge technique.
If you are building a new pipeline, as a section is completed, it is typically hydrotested. After hydrotest, many owners will dry the section and purge the atmosphere with Nitrogen. Often, these lines are not completely dry and the combination of water, oxygen and bacteria, can have a negative corrosion effect on this new steel, even if the line has a Nitrogen blanket.
Maintaining the Nitrogen can take time and be expensive, especially if the line will not be commissioned for a period of time. VCI can be introduced to the non-piggable segments as well as the piggable lines very cost effectively in most cases.
The VCI can then preserve the line from corrosion for many years. When it is time to put the line into service, there are options for removing the small amounts of VCI slurry, or in some cases, simply start pumping the product. Similarly, existing lines can be preserved by VCI after cleaning.
How the pipe casing solution works ?
High Viscosity Gel Application
WHEN: For pipelines with a metallic short (i.e. casing in contact with the carrier pipe) or pipelines where a static fill anti-corrosion solution is needed. This also meets PHMSA requirements for a protection system that remains in place. HOW: The gel system is installed as a low viscosity slurry which sets up as a high viscosity gel. The VCI molecules volatize from the gel to protect the vapor spaces in the annulus. The SCI in the product neutralizes contaminants on contact. The gel system has advantages over the other two applications in that, as the gel sets up, it can bridge small penetrations and reduce the possibility of the solution leaking out of the casing. Converesely, it helps slow down the ingress of contaminants from the outside.
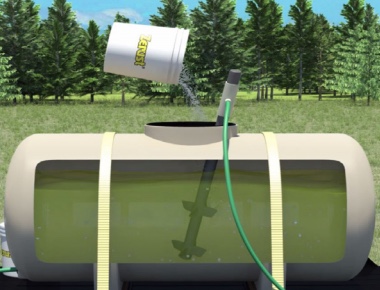
Gel System: Gel crystals are introduced prior to injection through the vent pipes.
Powder Application
WHEN: For pipelines without a metallic short, but for which providing internal corrosion protection is a good operating procedure, Zerust recommends the use of its dry powder inhibitor. As long as there is minimal water ingress (i.e. end seal integrity is maintained) the system will protect the carrier pipe from corrosion. HOW: A simple blower system is used to blow Zerust’s proven blend of Zerion powder inhibitors down into the pipe casing through the casing vent pipes. The Zerion powder is blown down the entire length of the annulus and settles on the bottom of the casing pipe. SCIs neutralize contaminant in the bottom while VCI volatizes to protect the metal surfaces in the vapor space. The entire annular space of the cased pipeline is protected.
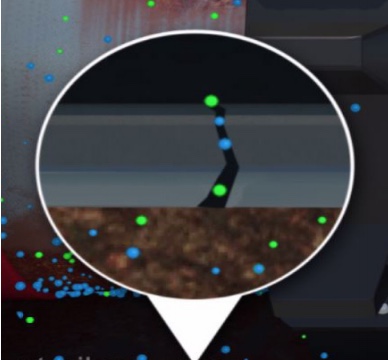
Inhibitors neutralize contaminants on contact and in the vapor space of the annulus. The amount of VCI required depends on the volume of the annulus and any contaminants that may be present.
Slurry Application
WHEN: For long lengths of pipe with varying elevations, bends and other geometric/dimensional parameters where a powder or gel is not feasible.
HOW: Zerust’s unique Zerion FVS is first mixed with water. Gravity or a low pressure pump is then used to inject the inhibitor slurry through the casing vent pipe into the annular space. The SCI in the product neutralizes contaminants on contact. The VCI molecules are released and equalize in the remaining vapor space, protecting both the exterior of the carrier pipe and inside of the casing. The entire annulus space of the cased pipeline is protected. The liquid injection is especially beneficial for longer casings as long as the integrity of the casing and end seals can be proven.
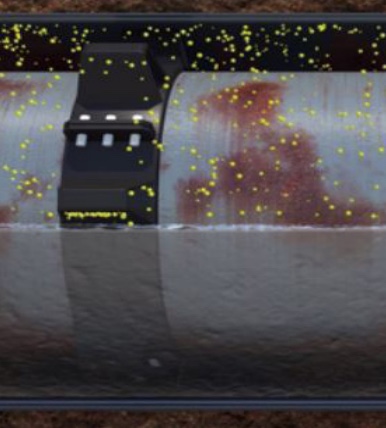
Zerust’s FVS product contains both VCI and SCI components. The SCI neutralizes contaminants on contact in the liquid phase while the VCI vapor molecules protect in the vapor space.